When device failures occur unexpectedly, the consequences for companies can be serious. Predictive maintenance offers a solution here. By detecting wear indicators and potential defects at an early stage, maintenance work can be planned in a targeted manner to prevent unplanned downtime and minimize operating costs.
In this article, you will learn how predictive maintenance works and what benefits it offers modern companies.
- In predictive maintenance, IoT, big data and machine learning are used for proactive and efficient
maintenance
of machines and devices to prevent breakdowns and increase their service life. - Predictive maintenance offers cost savings, increased efficiency, increased system availability and improved safety through early detection of problems.
- To successfully implement predictive maintenance, companies must carry out a comprehensive analysis of the current situation, select suitable technologies and partners and train employees in the use of the new systems.
Facility management
plays a central role in predictive maintenance, as it includes responsibility for the comprehensive support, management and technical administration of buildings and facilities
The essence of predictive maintenance

Predictive maintenance combines advanced technologies such as the Internet of Things (IoT) and machine learning to make precise predictions about the condition of industrial plants. In contrast to traditional maintenance strategies, which focus on
regular maintenance
or reactions to problems that have already occurred, predictive maintenance enables a proactive approach.
By continuously monitoring and analyzing sensor data, potential problems can be identified and maintenance work can be planned precisely when it is needed – and not when it is already too late.
Definition and objectives of predictive maintenance
Predictive maintenance is a strategy that aims to continuously monitor systems and precisely plan maintenance work in order to avoid unplanned downtime. In practice, this method enables more efficient maintenance of the systems.
The aim is to maximize the availability and performance of machines by preventing unexpected failures and extending the service life of the systems.
With the Wowflow app, you can plan maintenance work precisely, assign tasks and collaborate easily with external service providers.
Create a free account here
.
5 Advantages of predictive maintenance

The key innovations that make predictive maintenance possible are the Internet of Things (IoT), big data and machine learning – all important components of Industry 4.0.
IoT devices continuously collect data directly from the machines, while big data technologies process and analyze these huge data sets.
As a result, the predictive maintenance strategy offers a wide range of benefits, from increased efficiency and cost reduction to improved safety.
These are the biggest advantages of this maintenance strategy:
- Patterns are quickly recognized
Machine learning uses algorithms to recognize patterns and make accurate predictions about the condition of the systems. By detecting patterns at an early stage, companies can optimize their maintenance work and plan repairs efficiently. - Reducing costs and increasing efficiency
Instead of relying on regular maintenance intervals, predictive maintenance enables maintenance to be carried out as required, reducing the need for expensive emergency repairs. - Increase in system availability
By reducing unplanned maintenance and making efficient use of planned downtimes, companies can maximize their uptime. - Improved safety and risk management
By continuously monitoring machines, deviating behaviour and potential hazards can be detected at an early stage, minimizing the risk of accidents and breakdowns. - Consistently high product quality
In addition, regular condition monitoring and needs-based maintenance measures ensure consistently high product quality and prevent safety-critical quality defects.
Predictive maintenance: the role of facility management
Facility management is a key player in the successful implementation of predictive maintenance. It combines strategic management, technical expertise and a proactive approach to managing buildings and facilities efficiently and for the long term.
8 key tasks of facility managers in predictive maintenance

Professional maintenance requires professional facility management. These are the central tasks:
1. data collection: facility management is responsible for collecting and managing the data generated by various sensors and systems within a building. This data is the foundation of predictive maintenance strategies, as it can be used to derive patterns and predictions.
2. condition monitoringFacility managers continuously monitor the condition of the technical systems and infrastructure. You are therefore able to recognize when maintenance is required before actual failures or malfunctions occur.
3. use of technology: As part of facility management, technological solutions such as building automation and management systems are implemented, which are necessary for the implementation of predictive maintenance. These technologies make it possible to make precise predictions about the maintenance requirements of the systems under management.
4. cost-effectiveness and increased efficiency: Predictive maintenance enables cost- and resource-efficient building management.
building management
. Facility management aims to reduce operating costs and extend the service life of facilities, which is supported by preventive measures.
5. risk management: Facility management is responsible for risk management within a building or facility. Predictive maintenance helps to minimize risk by identifying potential faults and failures before they lead to safety risks or costly repairs.
6. planning and resource management: Effective maintenance planning requires a forward-looking definition of priorities and resources. Facility management uses the findings of predictive maintenance to plan staff and materials efficiently.
With Wowflow, you can plan your maintenance tasks and manage your data easily. Use Wowflow here free of charge.
7 Sustainability: Facility managers are increasingly required to promote sustainable practices. Predictive maintenance supports sustainability goals by helping to save energy, reduce waste and avoid unnecessary emissions.
8. compliance with legal regulations: In accordance with the
operator responsibility
predictive maintenance guarantees that installations and systems in a building comply with legal requirements and standards. Facility Management organizes and monitors compliance with these regulations and thus avoids legal consequences.
Below you will find further practical examples for your maintenance.
Practical examples of successful predictive maintenance
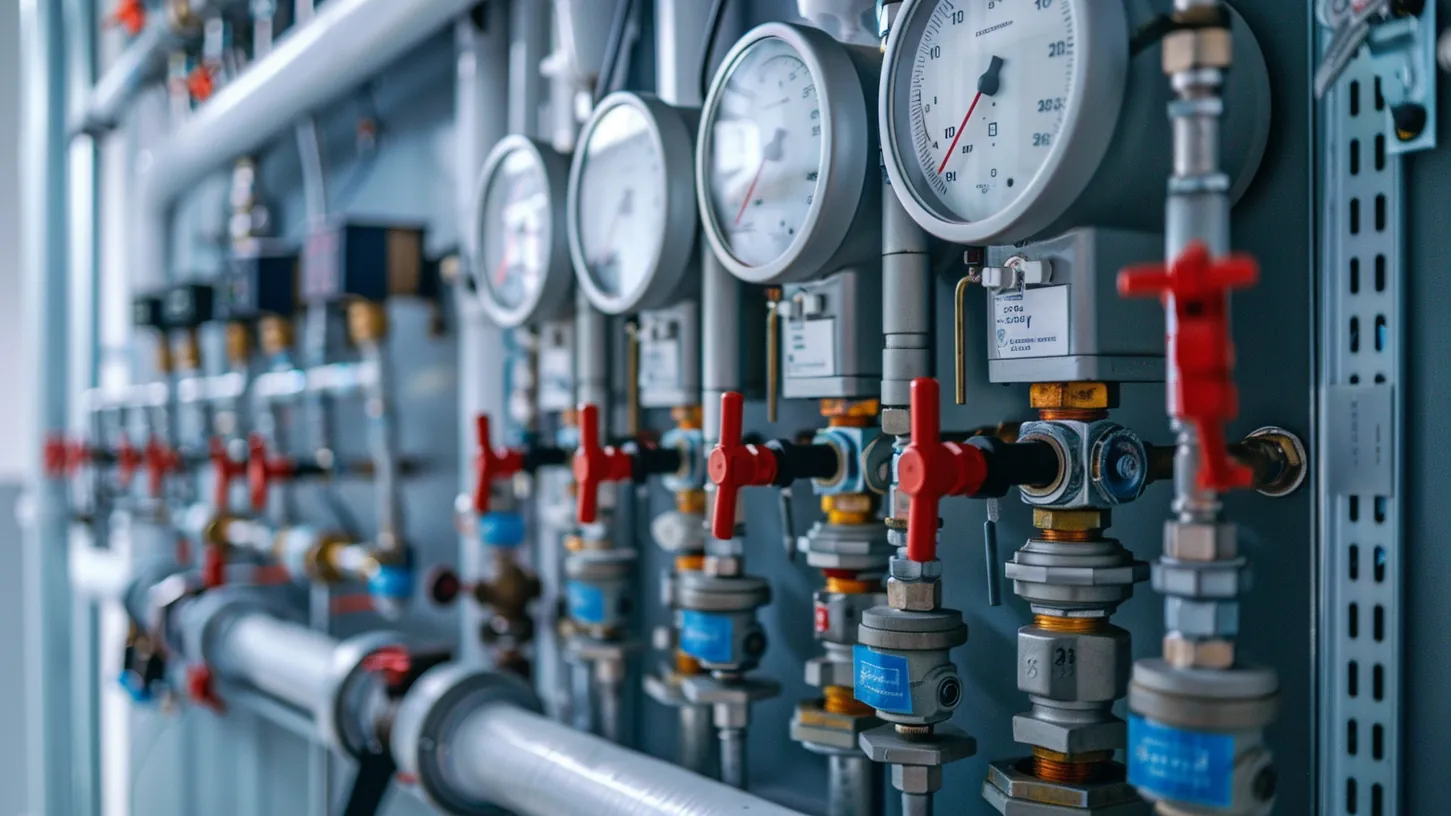
Predictive maintenance is already being used successfully in various industries and shows how the real-time analysis of machine data can bring considerable benefits. From the monitoring of heat pumps to the maintenance of high-speed trains – the application examples are diverse and demonstrate the effectiveness of this maintenance strategy.
Predictive maintenance in facility management
Predictive maintenance is used in facility management to optimize energy management, elevator maintenance and water management. By using intelligent systems and sensors, anomalies can be detected at an early stage and maintenance work can be planned in a targeted manner to prevent breakdowns and keep operations running efficiently.
With the Wowflow app, you can plan your maintenance work clearly and intuitively. Try it out for yourself!
Predictive maintenance in the automotive industry
In the automotive industry, predictive maintenance helps to optimize vehicle maintenance and make production processes more efficient. Sensors and real-time analyses make it possible to detect and replace defective parts at an early stage, which prevents expensive repairs and ensures the quality of the vehicles.
Optimization in the energy industry
Predictive maintenance also plays an important role in the energy industry by helping to increase efficiency and reduce costs. Utilities can use this technology to avoid costly repairs while increasing customer satisfaction by minimizing unexpected outages.
2 key challenges of predictive maintenance
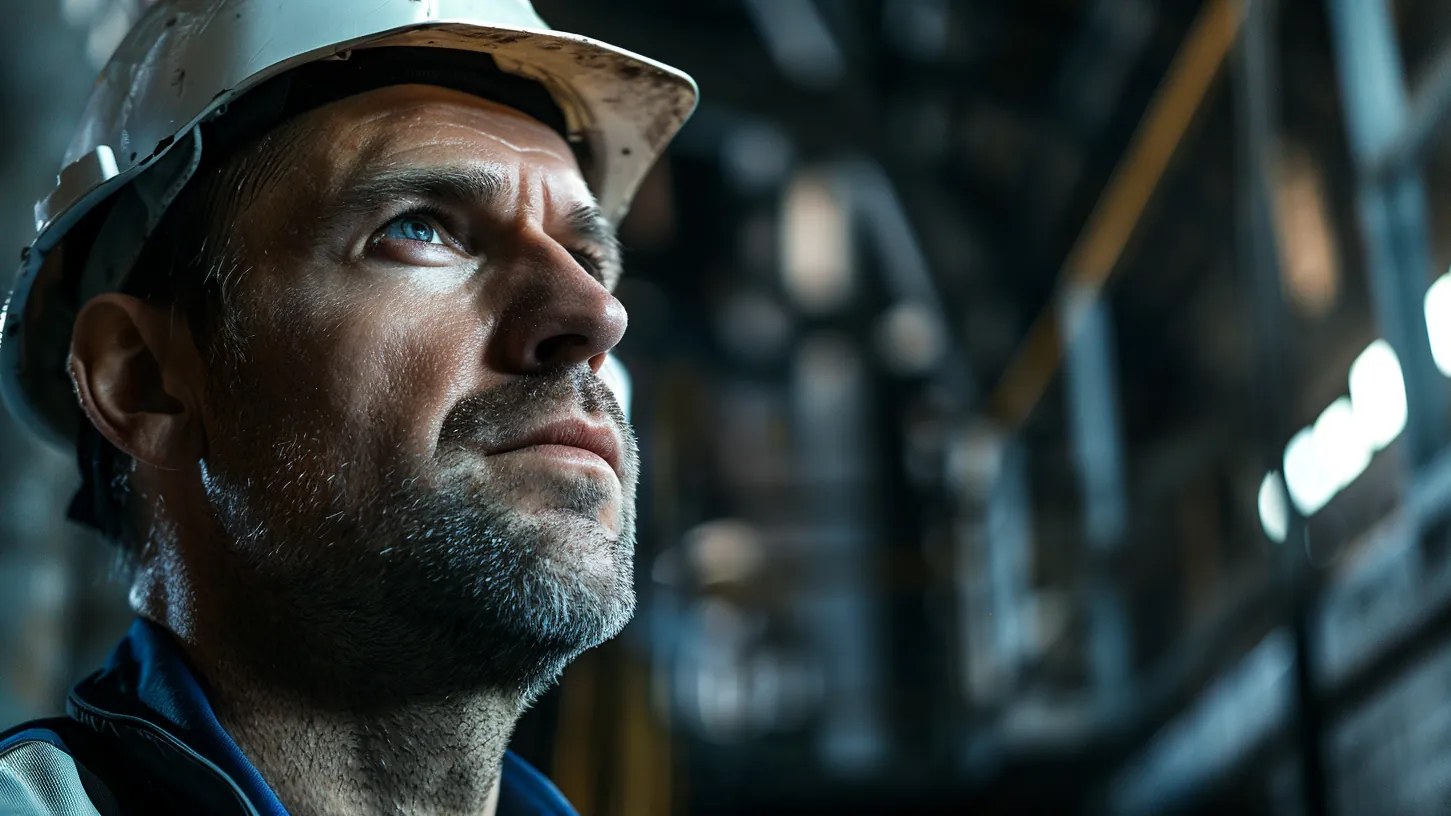
Despite the many advantages, there are also disadvantages to implementing predictive maintenance. The quality and relevance of the data and the development of the necessary technologies and expertise can be a challenge for companies.
Internal resistance to changing existing processes can also make implementation more difficult. In our opinion, these are the main challenges:
- Data management
Data protection and data sovereignty are of paramount importance in this maintenance strategy in order to handle company data securely and avoid risks such as security breaches or industrial espionage.
The handling of heterogeneous data sources and the consolidation of data pose further challenges. - Integration into existing systems
The integration of predictive maintenance data into existing systems requires special IoT hubs and gateways for data transfer. It is important that companies retain control over their data and integrate it securely into the cloud or in-house systems in order to meet individual requirements.
3 steps to implementing predictive maintenance

To successfully implement predictive maintenance, companies need to follow a series of steps. These include:
- Identification of critical systems
- Analysis of the current status and definition of objectives
- Selection of suitable technologies and partners
- Employee training and change management
Analysis of the current situation and definition of objectives
Before maintenance strategies can be implemented, a thorough analysis of the actual condition of the machines is required. Targets should be set based on the frequency and severity of machine malfunctions.
Selection of suitable technologies and partners
Choosing the right technologies and partners is crucial to the success of predictive maintenance. Companies should set specific security requirements and pay attention to contractual assurances and certifications.
The integration of predictive maintenance solutions should promote the return on investment and support sustainability goals.
Training and change management
For the successful implementation of maintenance strategies, it is crucial that employees are trained accordingly and have the ability to make data-driven decisions.
Change management is also important in order to adapt existing workflows and effectively integrate new processes and technologies.
Summary
In this article, we have discussed the importance of predictive maintenance for Industry 4.0, the associated benefits, practical examples and the challenges and steps for implementation.
Predictive maintenance is a key element in optimizing operating processes and ensuring system availability and efficiency. Companies that use this maintenance strategy can increase their competitiveness and prepare themselves for the future.
Frequently asked questions
What maintenance measures are there?
There are different types of maintenance measures, including reactive maintenance, active maintenance and predictive maintenance, as well as other strategies such as damage-based, preventive and condition-based maintenance. The maintenance process also includes inspection, servicing, repair and improvement to ensure the optimum condition of systems.
What is preventive maintenance?
Preventive maintenance involves regular maintenance work on systems or machines in order to identify and rectify potential problems before they lead to malfunctions. It serves to prevent failures.